Trends On The Horizon: Workplace Health and Safety Training Industry
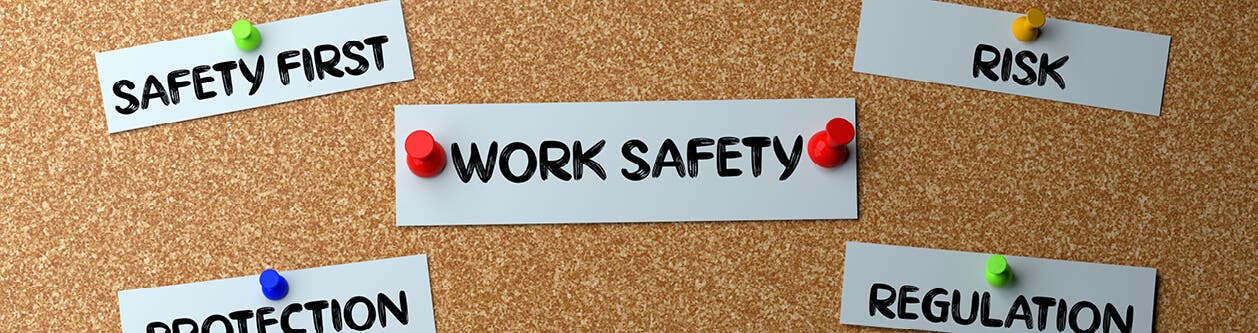
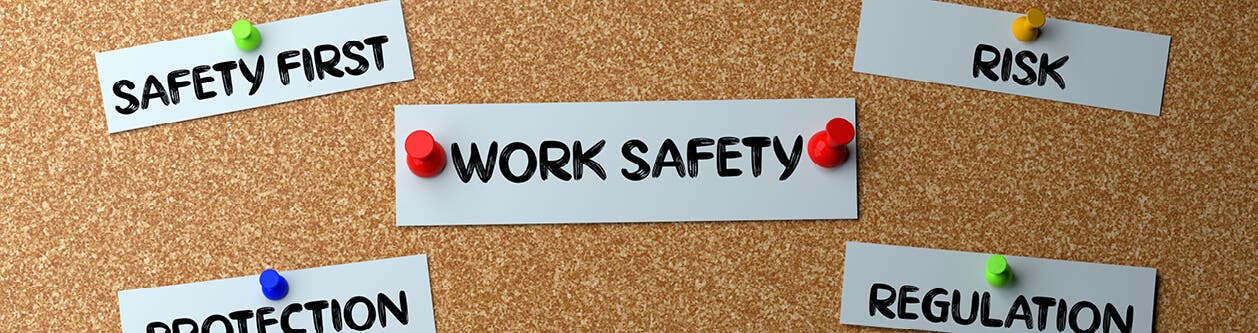
Paul Colangelo, STSC, CHST, CET, CRIS, is national director of compliance programs at ClickSafety, with 25 years' experience in occupational safety and health (OSH) and more than 17 years’ experience as an accredited Occupational Safety and Health Administration (OSHA) outreach trainer. This interview article was originally published in the September 2017 issue of Professional Safety, published by the American Society of Safety Engineers (ASSE).
Paul shares his insight on safety training, which is an important component of any OSH program. Tools such as ANSI/ASSE Z490.1 and applying microlearning concepts can help trainers be more effective.
PS: Employee training is a key component of performing work safely. What does a company’s investment in training say about its view of safety?
Paul: You can look at it from both sides, company culture and regulatory compliance. From OSHA’s perspective, training is an employer requirement. Per OSHA’s recommended practices for safety and health programs, training is one of the seven core elements. In the past, many companies wanted to simply meet the bare minimum in terms of training. Today, more companies are making sure their training is ongoing and effective. They are no longer satisfied with saying “our employees are trained.” They are taking steps to ensure that the quality and effectiveness of those programs are continually measured and evaluated from direct feedback by supervisors and employees.
PS: Do you see the same trend among small- and medium-size companies?
Paul: In terms of budgets, medium-size and small companies are more restricted, but they understand the importance of training. Many smaller companies are under a subcontractor umbrella of some larger companies. We have seen a shift in that some larger companies are now making their training programs available to their subcontractors.
PS: What makes for an effective employee training program?
Paul: The game has changed for safety professionals, regardless of whether they deliver the training themselves or hire third-party trainers. Training is no longer just about selecting training topics. It is about organizations making sure employees have the proper training for the hazards they will face each day, and making sure the learning result is demonstrated in the field. This is where it is advantageous for a company to select a training provider that not only offers training but also is willing to help the company structure an effective program.
PS: ASSE is secretariat of ANSI/ASSE Z490.1-2016, Criteria for Accepted Practices in Safety, Health and Environmental Training. How has it affected the quality of OSH training?
Paul: Z490.1 is another game changer. It requires a company to think beyond a trainer’s ability to use his/her background in terms of a certain trade, such as, for example, an electrician teaching about electrical safety. When vetting a trainer, an organization must look beyond the trainer’s experience in a certain trade discipline and ask bigger questions: Is this trainer skilled in adult learning? Does this trainer know how to perform a proper audience assessment? Does s/he know how to develop learning objectives? Does the candidate know how to structure a classroom that will support the learning environment? In addition, since most workplaces have a mix of older and younger workers, a potential trainer must understand what types of media and technology will be most effective. Again, saying that your employees are trained simply is not enough.
PS: How can a company assess training effectiveness?
Paul: Historically, the answer has been quizzing and testing. However, we have learned that someone can sit through a class, not absorb much content, yet still pass a quiz or test. Once employees leave a training class, regardless of how they performed on a quiz or a test, just having that completion certificate is not enough. A more effective way to demonstrate effectiveness has two avenues. The first involves frontline supervisors. The company wants to be sure that what employees learned in their training class is demonstrated on the job. This is where feedback from frontline supervisors is critical. The second avenue is ongoing knowledge assessments, which involves microlearning. Suppose students complete initial training on an OSHA Focus Four topic such as fall protection. After the program, trainees receive a daily question via a mobile device. It only takes maybe 30 seconds to answer the question. The company can track factors such as how long it took a student to answer and whether s/he answered correctly. This can occur over 6 weeks, 6 months or whatever period the employer sets. This microlearning approach keeps the initial learning fresh and measurable.
PS: Microlearning is a popular topic. How is it being applied to worker safety?
Paul: Microlearning is actually a newer technology based on an old platform—toolbox talks. Toolbox talks are an informal training approach that gathers employees together to briefly discuss a specific safety topic. For example, before a project starts in the morning, the foreman selects a topic, such as hard-hat safety, and delivers a short, informal session with a few key points. One principle of adult learning is that adults tend to learn better in small, informal environments. People also seem to absorb smaller bits of information more easily.
PS: Are newer technologies such as virtual reality and augmented reality playing a role in micro-learning as well?
Paul: Interestingly, ASSE is developing a new standard, ANSI/ASSE Z490.2, on virtual training, so these technologies are coming on quickly for OSH trainers. When you consider the different media available, whether it is instructor-led, online or blended learning, virtual training is a natural progression. This is especially true as the workforce continues to become more diverse, and as younger people enter the workforce. Most young workers started learning on computers at a young age. They often prefer virtual media that are interactive and that incorporate interactive elements.
PS: What key questions should OSH professionals ask when seeking to partner with an online training vendor?
Paul: One of the first questions should be whether subject-matter experts are developing the programs. I would certainly lean in the direction of a credentialed safety professional who has researched the programs to ensure that they comply with the latest regulation, are routinely audited, and are kept fresh and up to date. You also want to assess the vendor’s learning management system. Be sure to ask about its scalability, user experience and integration abilities. Also, customer support is a major element. The vendor should stand behind its programs. Look for a vendor that offers more than simply programs. You want a vendor that will help the company structure specific training curricula for workforce requirements.
PS: ClickSafety exhibited at ASSE’s Safety 2017 conference and exposition. What were some questions from attendees?
Paul: Many safety professionals wanted to know about our new programs. For example, this year OSHA had many regulatory changes, such as Subpart D 1910 on walking/working surfaces. OSH professionals wanted to know what their compliance training requirements included. Many asked whether our programs are approved by certain regulatory bodies. For example, when dealing with the Department of Defense projects and associated EM 385-1-1 safety and health requirements manual, it is important to ensure that the OSHA 10- and 30-hour programs your employees complete will be accepted. Another big question involves continuing education units, or CEUs. ClickSafety is an IACETauthorized provider, a move we made 3 years ago to meet client demand. Interestingly, the IACET process goes hand-in-hand with ANSI/ASSE Z490.1 because it truly measures and mandates how our programs are assessed, designed, developed, implemented and evaluated.
PS: How do you identify topics that are of interest to industry?
Paul: That is one of the huge benefits of being at events such as ASSE’s annual conference. We can network one-on-one with practitioners who discuss their specific challenges. In the past few years, we have also worked with clients to develop much more custom content. This includes orientations that companies use to onboard new workers. Safety and health should be part of that process so that these new workers know what to do if they are injured or encounter a hazard. More clients recognize that it makes sense to integrate technology-based solutions into this process.
PS: What other trends are on the horizon for the training industry?
Paul: One of the first things is mobile technology. We live in a world where everyone wants immediate and on-the-go training. The big concern is making sure quick and easy does not displace training quality and effectiveness. OSH professionals need to consider how these technologies might benefit their workforce.
PS: ClickSafety is a major sponsor of ASSE. How did that relationship come about?
Paul: When we looked at how best to launch the ClickSafety brand in the industry, what better place to start than ASSE, the oldest and most storied organization for safety professionals and highly recognized and attended professional development conference.
PS: Final thoughts?
Paul: During Safety 2017, our team spoke to numerous safety professionals from different industries: construction, transportation, warehousing, mining and so on. And we also spoke to many health professionals. These conversations remind us that OSH professionals must not only address the hazards that injure workers, but also the many hazards that can make workers ill, such as asbestos and lead. We’re all in this fight together to promote a safer and healthier work environment.